CleanTech Partner
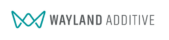
3D printing when imperfections cost lives
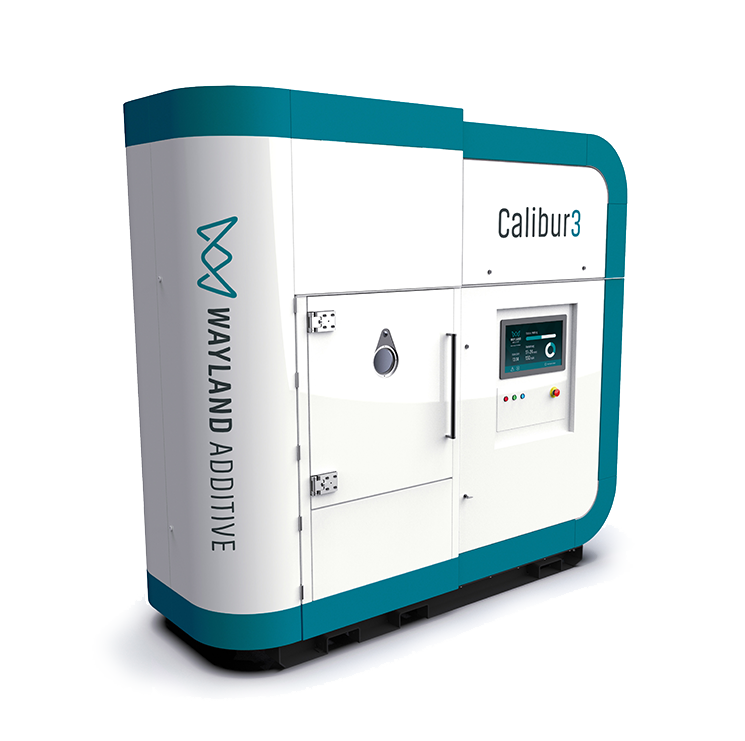
immersive kick off
hours
hiring budget saving
- UK
- Germany
Overview
Wayland Additive – 3D printing when tiny manufacturing imperfections cost lives
When it comes to metal manufacturing for the defence and aerospace industry, imperfections, measured in nanometres, are intolerable. Lives are literally at stake and scrutiny around the engineering technology couldn’t be sharper.
Scaling and commercialising this ground-breaking technology was the top priority for the 13 founding members. Now 52 staff, Bond was brought in to prepare Wayland Additive for rapid growth and put them on a trajectory towards a £1bn valuation by 2030.
Whilst the technology was exceptional there was no dedicated HR function and a people strategy was yet to be defined for that journey.
Laying the crucial foundations for Wayland Additive to date has involved leading it internally and of course, delivering it.
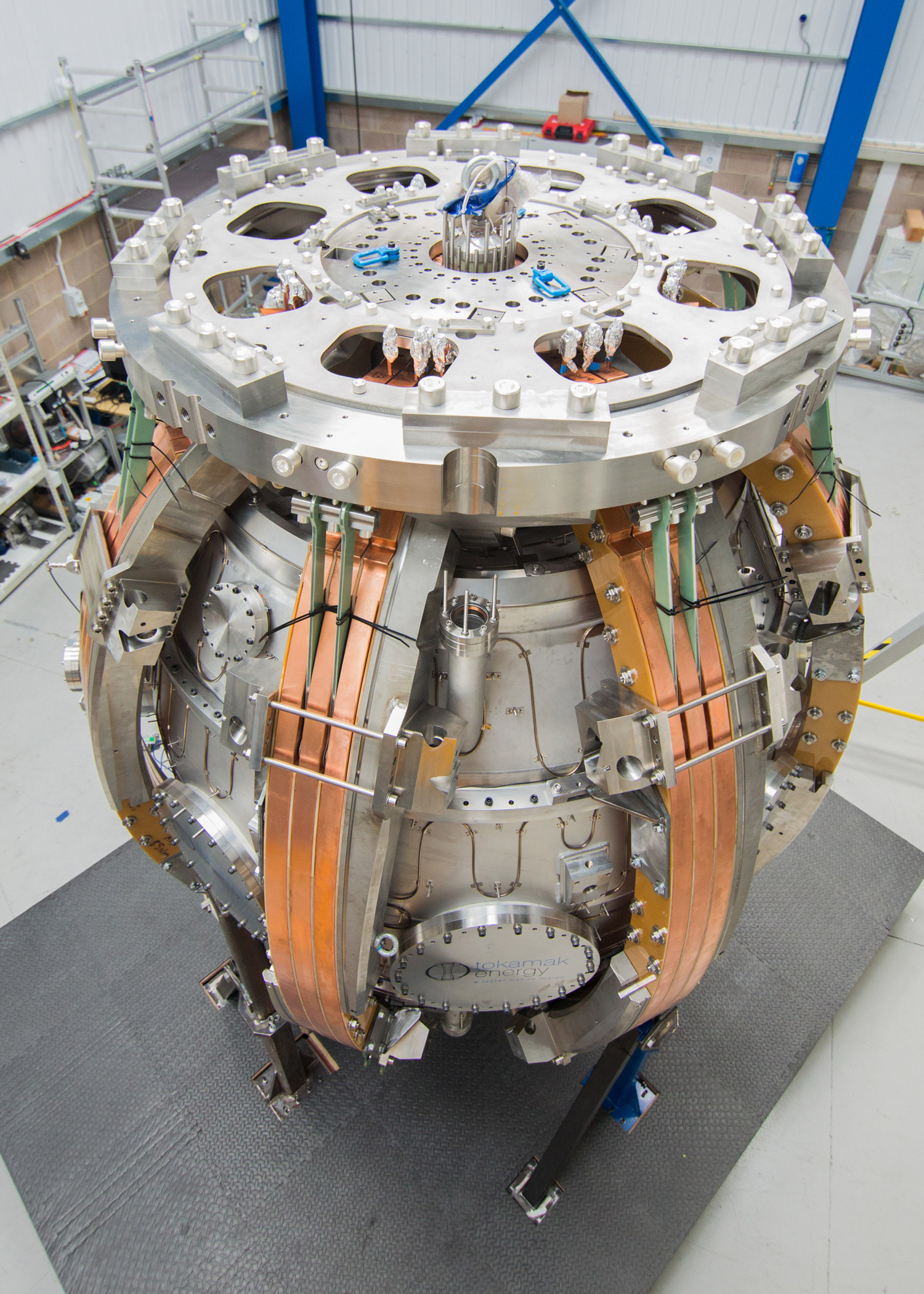
The first 72 hours:
Kicking off via a discovery deep dive on the first visit to the site
- Conducted a business-wide stakeholder engagement (11 senior leaders across all business functions)
- Co-ordinating a holistic view of hiring demand
- Prioritising the roles, reaching an agreement and holistic budget setting
- The result of this exercise alone saving £250k of hiring from taking place too soon
- Centralised co-ordination of people hiring efforts the big win
Following on from that in-depth discovery:
- Bond became the Talent function and shaped their first HR function
- Implementing a distinct process for end-to-end recruitment
- Job role sign off
- Centrally co-ordinated job description writing
- Clear interview process to ensure a strong cultural fit
- Relocation policies
- Rolled out Wayland Additive first Performance Development Plan process
- Introduced McQuaig personality insights to support finding and retaining the right people for scale
- Conducted a salary benchmarking exercise for entire business + and costs of living inflation analysis
It’s all about relationships:
Our Talent Partner has been considered a Wayland Additive employee as a result of relationship building capability
- Bond spent a week with the senior leadership team in Germany at formnext (Additive Manufacturing Expo) representing Wayland Additive and helping build their network
- They form part of the Wayland Additive official company org structure too
The road ahead together is an exciting one with key strategic hires and double-digit headcount growth planned for 2023
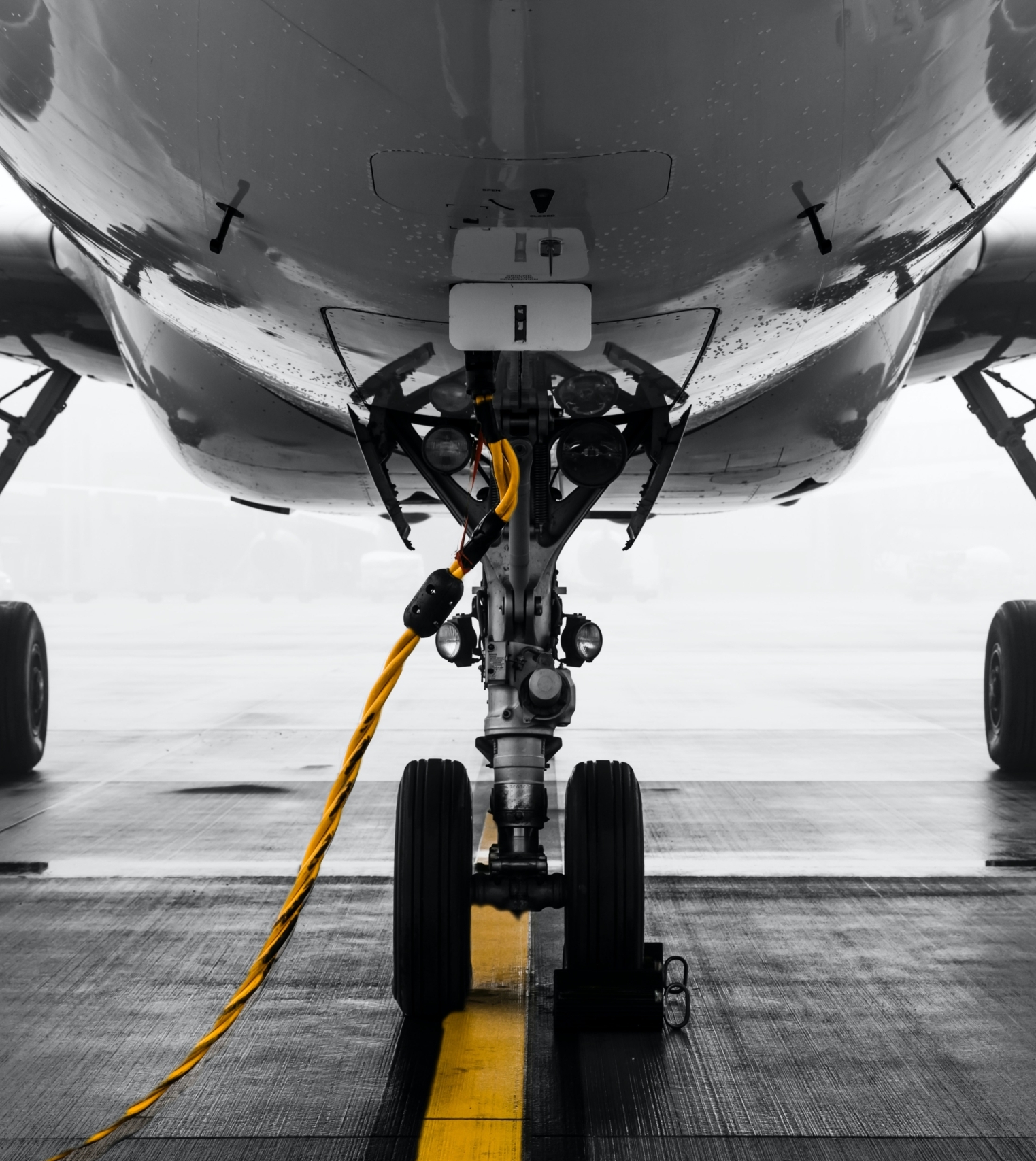
About working with Waylands Additive
At Bond, we are passionate about clever technology and align ourselves with partners who are helping un-fuck our planet. After all, there is no planet B.
The ground breaking additive manufacturing process, NeuBeam® , neutralises the electron beam (eBeam) powder bed fusion (PBF) process. Offering greater stability and enabling metallurgical requirements to be tailored to the specific metal production applications.
It has been patented in 7 counties and is awaiting sign-off in a further 5.
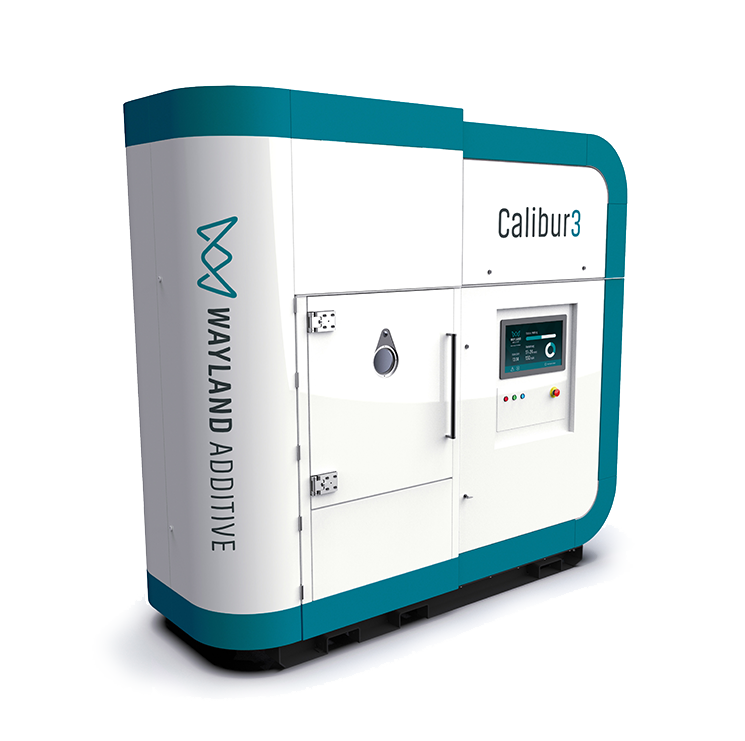
Testimonial
“Bond’s recruitment solution is helping Wayland to track its growth plan without overburdening the existing staff with recruitment tasks. By defining a company wide recruitment process Bond has been able systemise what had been previously an ad hoc internal process, significantly reduce the exposure of staff to opportunistic enquiries from other agencies and reduce the time spent internally on recruitment. Bond’s selection and screening process has resulted in well suited candidates for interview with minimum internal disruption”
Will Richardson
CEO